How to develop a tyre - targeted research, a range of materials and a clear definition of every aspect of the process are the crucial steps to take when creating a new product.
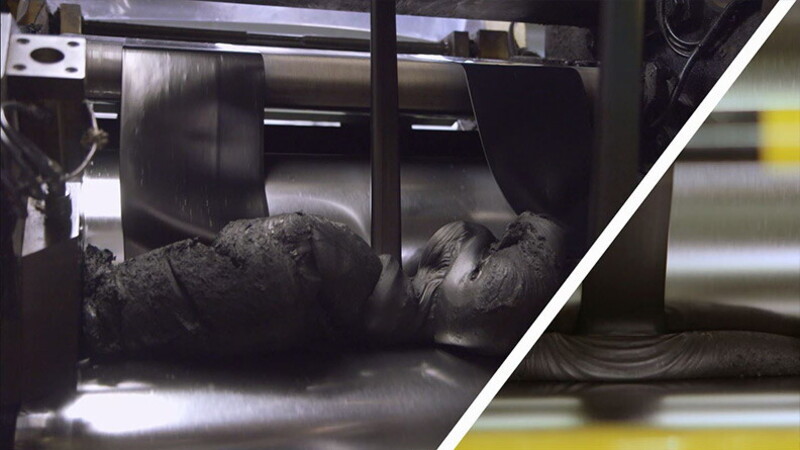
There are various stages used to create a compound: a mixing of different types of rubber, then assembly, where different components are applied, followed by a honing process which brings an increasingly defined form to the tyre.
The process is made up of a series of well-defined steps, all carried out with the utmost care, and during the various procedures a huge number of substances and types of rubber may be used, as well as metallic fibres - often in large amounts - which can amount to a total of 200 different materials and substances, such as additives, used in the production phase together with different types of rubbers, both natural, obtained by removing the latex from specific plants, and synthetic. In terms of its molecular structure, natural rubber is 94% polyisoprene and linked to protein, fatty acids and other elements, and is easily manipulated at high temperatures, though it has somewhat modest mechanical properties as a result of the rather weak force which holds the polymers together. Synthetic rubbers, on the other hand, are made through the process of polymerisation. For tyre production, the main ingredient is polybutadiene, a butadiene polymer used in the polymerisation of the compounds.
In the first phase of production, more than thirty different types of both natural and synthetic rubber may be used to make and define a new tyre. Materials which have unique, specific properties which differentiate each and every product. The compounding and mixing phase makes use of these various natural and synthetic rubbers, fusing and kneading them together in huge mixers. The careful elaboration of the various materials results in a smooth and compact compound. The next phase is assembly, where the characteristics of the manufactured tyre are stabilised, and which is carried out according to precise qualitative criteria and specific characteristics in terms of resistance and road behaviour, always keeping to the highest safety standards.
The assembly is a process with several distinct phases. These processes use a rotating drum, to which the materials used to shape the new tyre are attached. First, a layer of synthetic rubber is applied, which makes up the air chamber for the most advanced compounds which, unlike in the past, no longer need more than one air chamber. Once this has been complete, the process continues with the carcass; essentially the armour which holds and begins to further shape the product, made of rubber and a dense, metallic weave. Then comes the addition of the beads, which are joined to the carcass. These are metallic steel bands which, as well as ensuring the tyre is waterproof, also make sure it retains its circular shape.
The shaping of the tyre proceeds with the application to the sidewalls of rubber bands of certain characteristics of resistance and flexibility to deformations, and which must support the elevated forces to which the tyre will be subjected in this sensitive pressure area. As the sidewalls of the tyre take shape, the marks also appear which enable the identification of the tyre type. The true form of the product is then defined, as the zone adjacent to the cylinder is inflated and the compound takes shape. To this structure is added the covers at the summit, made up of criss-cross patterns which shape the carcass, before the positioning of the base which accepts the tyre tread: the section which will make contact with the ground and which characterises each specific kind of tyre. From a more or less well-defined tyre tread, it is possible to understand the nature of the tyre's performance.
Even with the various components in place, the shaping process is still not complete Only after the vulcanisation phase, meaning the heating of the prepared base in a specially-prepared mould, is it possible to have a clearer idea of the newly-engineered product.
The so-called "raw tyre" is placed in a specially-prepared mould, as we said above, for the time necessary for it to be cured, shaping and solidifying each side. Then centrally, a membrane moistened with hot water using pressure brings the unrefined material towards the walls of the mould and the heat then does its work. At 150°C the true vulcanisation process of the compound begins. The addition of sulphur consolidates the polymer lattices, and the tyre acquires its elastic properties, in addition to its already defined form.
Once the vulcanisation process is finished, next comes the phase which enables you to understand if the finished product conforms or otherwise to that which was planned: the control stage. It is a verification process made using a special X-ray instrument and a careful analysis by specialist inspectors in order to determine, thanks to the support of highly accurate technology, if there are any imperfections. If there should be even a minimal or imperceptible distortion from the qualities desired, the product will fail the control test. If not, the product is labelled complete and passes to further tests on the road.