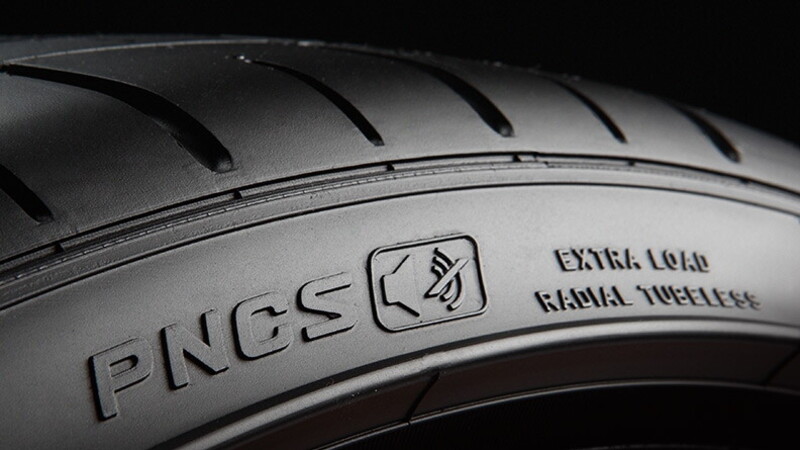
Rolls-Royce used to say that the only sound passengers would hear as they were transported in serene comfort was the tick of the dashboard clock. Ticking clocks are a thing of the past, but the challenge of making a car as quiet as possible remains. It's no fun taking a journey when no one can make themselves heard. And traffic noise is widely regarded as pollution for people who live near busy roads or in a city. But it is a tricky problem to solve.
The sounds a car generates are produced by both the engine and the tyres. Recently, much work has been done on new ways to reduce the noise that tyres give off. And that's for one simple reason, says Professor Ulf Sandberg, senior research scientist at VTI – Sweden's National Road and Transport Research Institute – who literally wrote the book on the subject . “You only hear tyre and road noise in an electric car,” he says. “There might be some hum from the motor but it's mainly the tyres.”
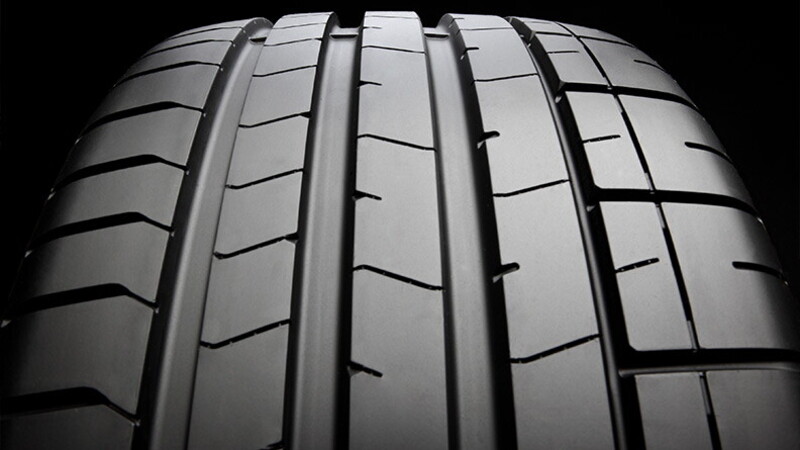
A lot of the noise that tyres generate comes from air being squeezed or “pumped” in the treads as the wheel rolls. In most tyres, tread grooves run around the tyre as well as across it. When rubber meets the road that squashed air in the long runnels is forced out through the treads cut across the width, producing that characteristic roar. It acts as a very efficient amplifier for the cacophony that tyre-road contact creates. The noisiest tyres generate about 70 decibels (dB) of noise; on poor roads the racket can be even louder.
Some tyres are notorious for being noisy. One, used widely in North America in the 1970s, was dubbed “Singing Sam” because of the distinctive – and distracting – tone it generated while driving.
Learning from… goats
Tyre makers have long experimented with different tread patterns to counteract this effect and have enjoyed some success in reducing it. More recently, Chinese researchers have put microscopic bumps in the walls of treads to disrupt airflow and limit the pumping effect. Kumho has gone as far as using tread patterns modelled on the hoof-prints of mountain goats to make quieter, grippier tyres for off-road vehicles. Others have created voids and pores in the rubber beneath the treaded layer in a bid to tackle the problem.
Pirelli has also been experimenting with tread patterns. Its latest P Zero tyres for the prestige and premium sectors have more grooves and deeper and wider channels on the surface. This helps deliver safer and more stable braking in wet conditions and it also helps reduce the noise heard inside the car. The transverse grooves are arranged in a deliberately out of order sequence to disrupt the noise generated by airflow and distribute the sound over a number of different frequencies, minimising its volume.
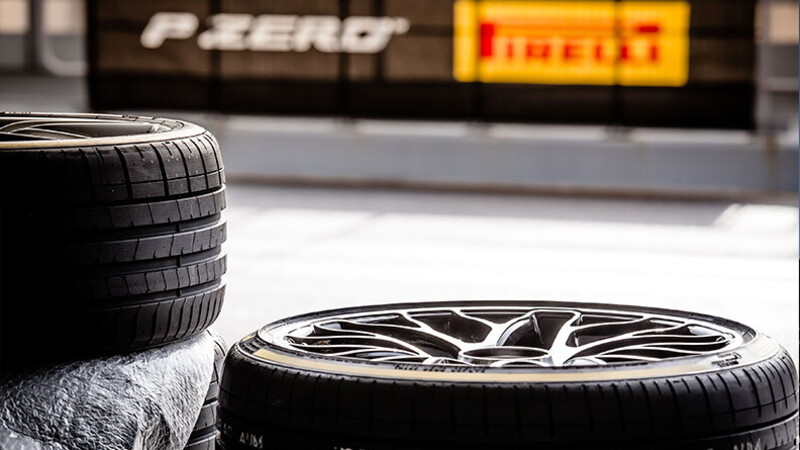
But Prof Sandberg, who's also involved in work with the European Union to standardise measurements of tyre noise, says there are other sources of noise, too. The cavity inside a rubber tyre and its metal rim resonate at very similar frequencies – so much so that they act as reinforcing amplifiers. Such a phenomenon can often be heard in the cabin.
To cut one source of this sound, some tyre firms – including Pirelli, Falken and Continental – have lined the internal air cavity with polyurethane foam or other materials that act as baffles and hinder the resonance. The Pirelli Noise Cancelling System gives a reduction in noise of between 2 to 3dB.
The price of fashion
And then there is the role that fashion plays. “In the last few years it has been popular to use wide tyres and they have grown wider and wider over time,” says Prof Sandberg. “Some people think that if a tyre is wide it looks sporty.
“This is a development that's been good for hardly anything. For rolling resistance, skid resistance and noise they have no advantage. It's just been driven by visual appearance.”
Car wheels that use thinner tyres that are greater in diameter would give a better performance on every count, he says. Prof Sandberg's research group at VTI put these ideas on trial by building a thin, wide solid wheel that mated the rim and tyre into one unit. A thin layer of treaded rubber is bonded to the outer layer of the composite wheel to give it grip. VTI tests showed it had very low rolling resistance and noise levels were about 10dB lower than conventional tyres, with the added benefit of being puncture free.
That low rolling resistance and space around the wheel's centre might also be a useful design for electric cars, adds Prof Sandberg. Low rolling resistance means electric cars can move for longer without needing recharging. And it might be possible to put small electric motors inside each wheel to replace the single source of power that battery-powered cars currently use. This would save on space and weight; key factors for cars that run on battery power rather than petrol.