Pirelli is one of their client companies and in 2013 signed a global agreement with DuPont Sustainable Solutions, with a special focus on a standard global approach to behaviour-related aspects of the safety culture in the Group. The program began in 2014, initially at sites in the United Kingdom, Venezuela, Argentina, Mexico, Turkey and Romania. In 2015, the program was extended to all the Group's production sites.
DuPont realized a number of years ago that a number of companies were very interested in how they implemented their safety culture so they created a safety service business to work with other companies. Over time the focus has expanded from purely worker safety to the broader area of sustainability. It is, in fact, a concrete example of how safety and sustainability can have positive bottom line impact. The corporate sustainability team works closely with the safety services business to coordinate latest approaches. The corporate sustainability team is headed by Dawn Rittenhouse who, in an interview with Pirelli.com, explained their thinking.
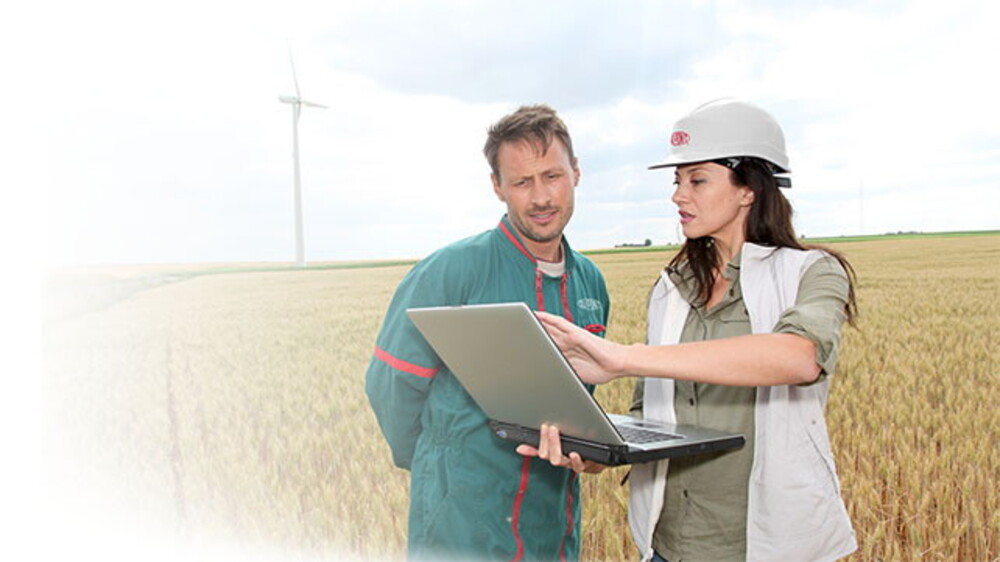
Rittenhouse has been with DuPont for over 35 years and with a chemistry and business background has primarily been on the business side. It is worth noting that she has no formal sustainability training and was given a very simple sounding, but business oriented task, by her CEO in 1998.
“He asked me to really understand what sustainability is and what it means for the company,” she said, adding “and I'm still working on it”.
The challenge, in her words, was creating growth and value for shareholders while reducing the environmental footprint along the supply chain – being a good citizen in all circumstances. One example was the solar panel industry. DuPont produces a number of materials that are used in the production of solar panels. The US EPA notes that the best approach to reduce environmental impacts is to extend the life of a product so DuPont's approach is to develop materials that extend the useful life the panels – therefore reducing waste while also reducing the life time investment that the customer makes.
Historically, DuPont was also well known for its excellent worker safety performance, particularly in manufacturing and this, as Rittenhouse explains, led to its evolution into a stand-alone business. “Because we were known for our safety performance, people started coming to us for help and over time we packaged this knowhow into a useful approach and provide it as a service to customers.”
Taking care of employees' safety, applies not only to behavior in the work place but also outside work. For example, for an office worker the most hazardous part of the working day is the often the drive to and from work, so this is a question of education which goes beyond strictly professional concerns. At Pirelli, for example, we now have posters around the HQ suggesting we walk up the stairs instead of taking the lift, telling us of the health benefits of this choice.
Under DuPont's guidance, Pirelli is implementing a 3 phase programme at its various sites over a period of 2.5 to 3 years. In the first phase, DuPont's methodology is used to assess the company's safety culture. This is done through interviews, surveys and visits to the shop floor or office. Based on its findings, an implementation plan, phase 2, is developed. This focuses on safety management, manager and worker training and coaching, implementation of safety tools, like safety dialogues and meetings. In the final phase, the effectiveness of the programme is evaluated. In locations where the programme has run its course the results have been positive. At the Pirelli factory outside Turin, the amount of time lost because of injuries fell from 128 hours in 2008 to 6 in 2014, the frequency of accidents fell by 95% and the severity also by 95%. This has clearly been a win-win situation for the company and its employees.
Rittenhouse notes that whereas once companies might have been driven more by external factors such as regulation, more and more they are motivated by their own interest and the bottom line. As a person who has worked in sustainability since 1998, she has noted this switch, even at events such as the recent climate conference in Paris.
“Years ago this would have been an event for governments with companies confined to the margins trying to understand what was going on and perhaps influence proceedings. Now companies are directly and pro-actively involved and making constructive contributions.”
“I also think that companies are starting to feel the effects of climate change now. It's not something 50 years away.”
Through their own behaviours, interaction with the supply chain and the possibility of finding new business opportunities in the climate change setting, companies can make real material contributions and accelerate improvements.
“Through their focus on materiality, companies can really make a difference in what is most important,” she concludes.