It's extraordinary to think that data coming from one machine at Pirelli's factory in China can improve the company's production process in Brazil… and on around the world.
Such is the potential of smart manufacturing.
Working practices related to production processes can – thanks to the harvesting of data – be applied immediately to resolve an issue in the same area at another plant.
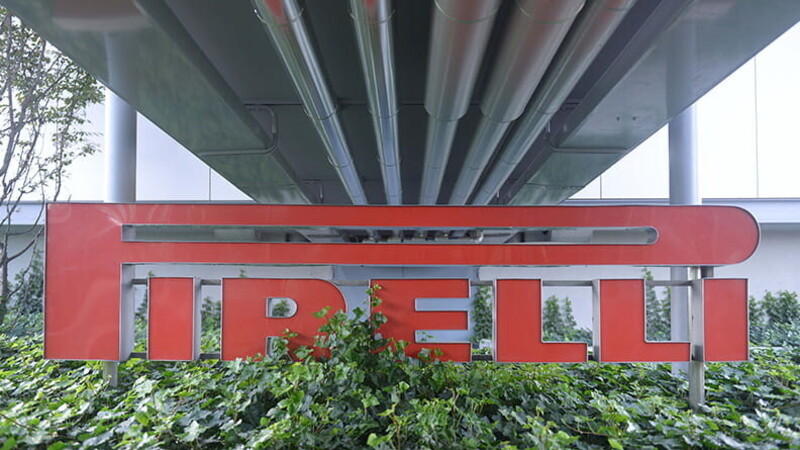
This is the inspiring principle behind the Pirelli Manufacturing eco-System. Thanks to the Manufacturing App, the various specialist professionals involved in production processes in different factories around the world can supply in real time all the manufacturing data for a product: from vulcanisation to assembly. This instant monitoring makes it possible to trace every single component from the compound room to the final quality-control check.
The sharing of best practice and relevant data enables Pirelli to bring continuous improvement to all its factories across the globe. This is the essence of Industry 4.0. A world that combines technology with people's skills: “Having connected factories and comprehensive data to process is pointless unless you have people capable of interpreting it,” explains Francesco Sala, executive vice president technical operations Pirelli. “If you want high-end products then you have to have the equivalent level of skills. At Pirelli, people play a crucial role and to manage departments that are entirely automated, you need some really intensive training.”
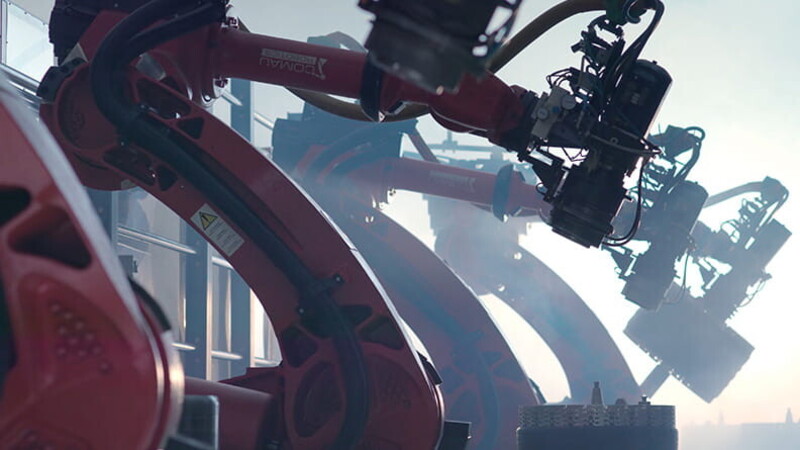
People's work, then, is still the element most capable of influencing Pirelli's production around the world.
Meanwhile smart manufacturing brings other benefits – it is an approach that feeds into the company's sustainability strategy. The eventual reductions in waste – and subsequently costs – will result in a smaller environmental footprint.