Businesses have always been heavily dependent on their supply chains, but the events of recent years have put these carefully balanced networks in the spotlight as never before. With a global pandemic, wars and unforeseen logistics shocks, many companies' supply chains have been disrupted. That's why Pirelli is focusing on building extra resilience into its own supply chain to help it deal with whatever shocks arise. Pirelli's head of supply chain, Luca Galantina, describes how the company is developing the supply chain of the future.
The entire global economy has recently been through a period where supply chains have been stressed. What has Pirelli learned from this?
I think we have learned that we live in a world of real unpredictability and the only way to deal with that unpredictability is to build resilience into the supply chain. Resilience is the new priority. We have to add resilience to the traditional priorities, which were efficiency and customisation. That is the way to guarantee sustainable growth and a maximum service level for our customers, and to deliver all this economically.
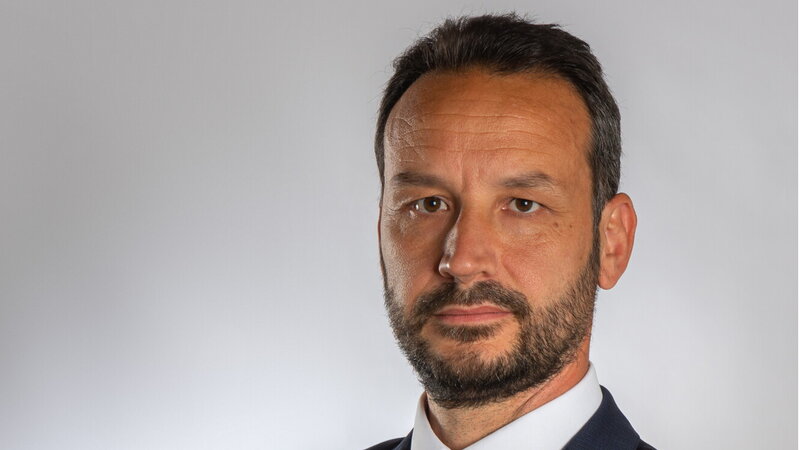
Is there ever a conflict between the need to build resilience and the need to keep costs in check?
They are not always in conflict when you think of the costs in a broader way. Take localisation: if you think only in terms of the lowest cost of production then you may decide that a distant source is the best solution, but that lowest cost today may eventually mean a higher total cost in the future because we also have to think of the additional costs of unexpected events. For example, if you have a sudden disruption of the supply chain, you may find you have to use premium express shipping to solve the problem with much higher costs than expected. So, you may have what looks like a very efficient low-cost supply chain, but if that supply chain is rigid and not resilient it could turn out to be very costly in the longer term.
What is Pirelli doing to make itself resilient to unforeseen shocks?
When we talk about unforeseen shocks this covers a wide range of events. Of course, there are major geopolitical events such as the Russia-Ukraine conflict or the recent Middle East situation, which have an impact both emotionally and on the business. But there are also other impactful shocks, like the incident in 2021 when the Suez Canal became blocked by a ship that had gone off course and become stuck. Then there are things that are the results of gradual climate change, such as the recent lack of water flow into the Panama Canal, which has reduced shipping traffic. And then there are supply chain stresses, which are consequences of economic changes such as the the sudden increase in sea freight rates we experienced in 2021 or the structural shortage of manpower in logistics, in particular of warehousing operators and drivers. To prepare for such unpredictable events, we are working in three main directions. First, localisation both in terms of production and sourcing of raw materials. Second, agility – if these events are by their nature unpredictable, then we have to be fast in detecting them and reacting to them. And third, risk management, which has to be a key part of our strategy both in terms of sourcing and the set-up of our supply chain.
What form will localisation take?
Localisation will considerably change the structure of our supply chain; in fact, we have a specific target in our industrial plan which is to achieve 90 per cent of finished product demand met by local production. From the sourcing point of view, we are asking our suppliers to increase their own level of localisation by reshaping their industrial footprint or distribution network. Clearly there are limits to localising sourcing, for example, the supply of natural rubber can't be localised in Europe or North America, but most other suppliers can expand their footprint to include countries where we have factories: a supplier with a factory in Japan or Indonesia could set up a plant in Mexico to supply our factory there. We are doing the same for our customers, the car manufacturers; we are expanding our global network to be close to their factories as well.
Are there opportunities to use new technologies like artificial intelligence (AI) to reduce risks?
I think the use of AI will be a game-changer. It is going to make the difference between being a leader and being a follower, and the leader will be the one who is able to implement AI effectively right through the supply chain. We are already working to implement AI algorithms that can scan the supply chain in order to detect and predict emerging problems and our ambition is to use prescriptive AI to not only foresee what will happen but also why it will happen and provide recommendations on how to act. There is no doubt that AI is going to become a critical factor in the level of supply-chain performance that we can deliver.
Pirelli has very ambitious targets for reducing CO2 emissions in the supply chain, targeting a 90 per cent reduction in Scope 3 supplier emissions by 2040. Have these targets changed your approach to supply-chain and suppliers management?
In order to meet these decarbonisation targets we have developed a very strong methodology for our work with our raw material suppliers. First, we asked them to provide us with the primary data of their emissions. Then we asked them to share their decarbonisation targets, preferably openly published and certified by the SBTi [the corporate climate action organisation, Science-Based Target initiative] as we are. Then we asked them to show us the projects they are going to implement to achieve those targets within the related timetable. Finally, we set up a governance structure to regularly assess this implementation plan in order to understand if everything is going as planned and to share additional ideas for decarbonisation projects. Looking ahead, a key driver for awarding future business to suppliers is their ability to match our sustainability requirements.
Looking at the Pirelli supply chain today, how do you expect it to be different by 2040?
2040 is not all that far away. But I think we can be sure that by then logistics will include a lot more electric power and other non-carbon fuels as well as more intermodal and maybe autonomous-driving transportation. I expect that in 2040 we'll have a self-driving supply chain powered by AI algorithms that will allow planners to secure optimal production plans and product availability allocation as well as high-speed multiple risks scenarios evaluation to prevent possible disruptions. Our people will be key to this transformation, particularly in terms of digital skills. We have to invest in their upskilling training path now and playing an active role in this journey. So yes, there will be a lot of change, for the better.