Pirelli's 2,000-strong Quality team is at the heart of the company's global operations. Its specialists are focused on delivering the highest-quality products and services for customers, harnessing the latest technology to enhance processes and control systems, and co-operating with Pirelli's many partners and suppliers throughout the value chain. Above all, everyone who works in Quality is part of the quest for continuous improvement and innovation.
Anticipating and exceeding customer and market expectations
Keeping ahead of ever-changing regulations, as well as constantly evolving customer requirements, is a big part of the job. Claudia , who works in the Quality management system department at Pirelli's Milan headquarters, says that the managerial side of the department's work revolves around three aspects: “First, understanding external requirements from international certification bodies, such as the International Organization for Standardization (ISO) and the International Automotive Task Force (IATF), as well as from customers. Second, translating these requirements into our own procedures and rules. Third, verifying that we are applying these rules by running internal audits. Only then can we show we are compliant.”
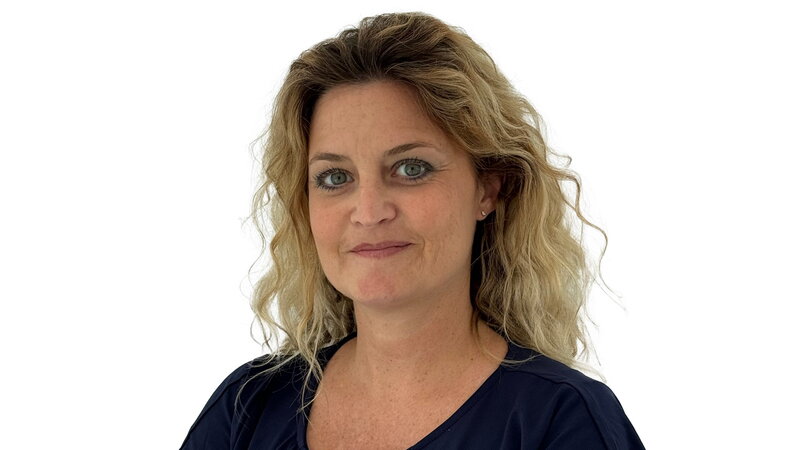
For Claudia, the constant awareness about the customer at the end of the supply chain concentrates the mind and guides everything she does. “It's very motivating,” she says. “If we failed to meet certification requirements, for example, we would have to stop manufacturing because we would be non-compliant, or we wouldn't be able to sell our products. So, I always feel a great sense of responsibility.”
Working closely with customers is fundamental to Quality and one of the major attractions for people working in the department. “You have lots of customer-facing interactions and the opportunity to develop your ‘soft skills' managing projects,” says Patrick, a Quality account manager based in Atlanta, Georgia, USA, who spent seven years working in Pirelli's motorsports team on research and development and product development before moving to Quality.
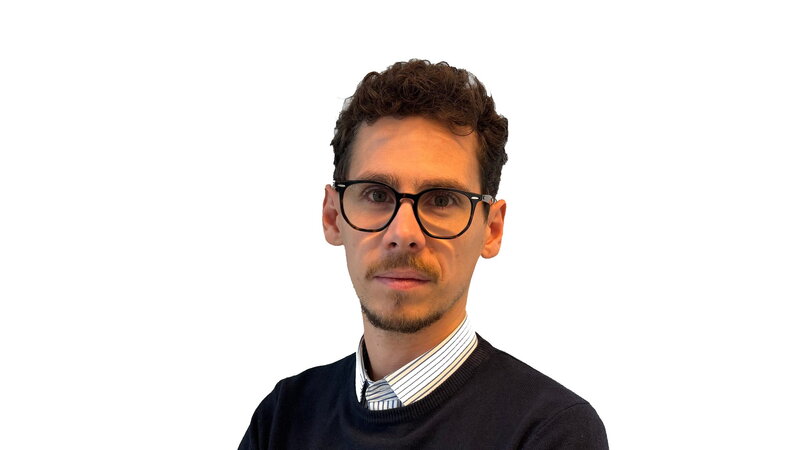
Accelerating the take-up of new technology
The ability to harness and accelerate the power of technology to transform how Pirelli delivers its products and services is both a necessity and an evolving challenge. “Most of the projects I'm working on depend on technology,” says Ozum. A chemical engineer by background, Ozum has spent 10 years in Quality and recently moved from Izmit, Turkey, to Milan.
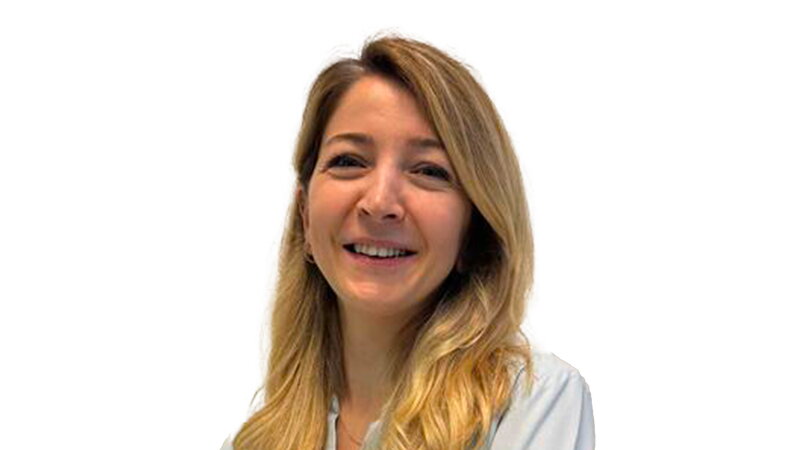
“One of the projects I'm following from the Quality side, and coordinating with factories, is related to product Quality control with an AI powered algorithm replacing the human eye,” she says. “This solution is beneficial to improve Quality output from the very beginning of the production. We've introduced this new technology thanks to excellent collaboration with suppliers.”
Manuel is been Pirelli's country Quality director for Mexico for 3 years, and now just joined the managerial team in the HQ As an industrial engineering graduate who also has a master's degree in finance, he spent eight years in Pirelli's manufacturing division before moving into Quality in 2019. He says he thrives on deploying the latest technology, which alerts him to any issues arising at the factory and gives him the speed to react.

“Digitalisation is fundamental for Quality,” he says. “It can help you prevent any problems, but also correct them. We have apps where I can see the results from the factory in real time, giving me a stream of indicators, including information about Quality output and yield. That kind of data is fundamental – and essential to taking decisions. What I like most about Quality is taking decisions.”
Supporting our partners
As well as working closely with customers, the Quality team also interacts with external partners all along Pirelli's supply chain.
“The key to our success is in the relationships we have with our partners and suppliers,” says Patrick, a mechanical engineering graduate. “ The original equipment manufacturers (OEMs) are key players and the tyres we produce are the culmination of long technical and quality partnerships.
But a focus on quality is not just limited to the business context, adds Patrick. It's an approach that helps you appreciate other aspects of the world too. “Once you get a deep understanding of quality as a “philosophy” it gives you a better understanding of everything around you,” he says. “You see a building or sit in a bus and you realise everything has been designed with a certain quality in mind, with certain procedures to make it the best it can be.”
Quality is built by people and their skills
It takes a wide range of skills to excel at maximising quality. In addition to being systematic and meticulous, you also need to be flexible enough to adapt to and deal with change. And perhaps, most of all, you need good interpersonal skills. For those who work in Quality, one of the most rewarding aspects is the way it brings you into contact with so many people – in particular those at Pirelli.
“For me one of the most enjoyable aspects about Quality is that you get to know so many people in the company,” adds Claudia, who joined the department after seven years working in human resources for Pirelli. “I know every function, every process. It's also a great opportunity to meet colleagues from other countries and cultures. Last year I went to Romania, Argentina, Germany and all over Italy. It's a great way to be a part of the company. You gain a very good global outlook.”