It may be a cargo ship stuck in the Suez Canal. It may be a pandemic that shuts down half the world's economy. Or it may be a war that nobody thought could happen. Surprises occur – and when they do, the impact on the supply of everything needed to keep a large international manufacturing company up and running can be immense. For the supply-chain manager, the challenge is to be ready for the unexpected – to plan, manage and, if possible, anticipate events well before they actually unfold.
For Victor, based in Sydney as supply-chain manager for Pirelli in Australia, supply chain is really an everything job. “Australia is not a large market, but that means you have to be involved in everything, you have to have a 360-degree view of the business,” he says. “I handle matters related to transport and the costs of distribution. I do forecasting, planning, market research, building up our understanding of the market in terms of what kind of cars are selling in Australia, what our competitors are doing and how we can grow. Plus, I handle every kind of request whether from customers or suppliers. So, yes, supply chain covers everything.”
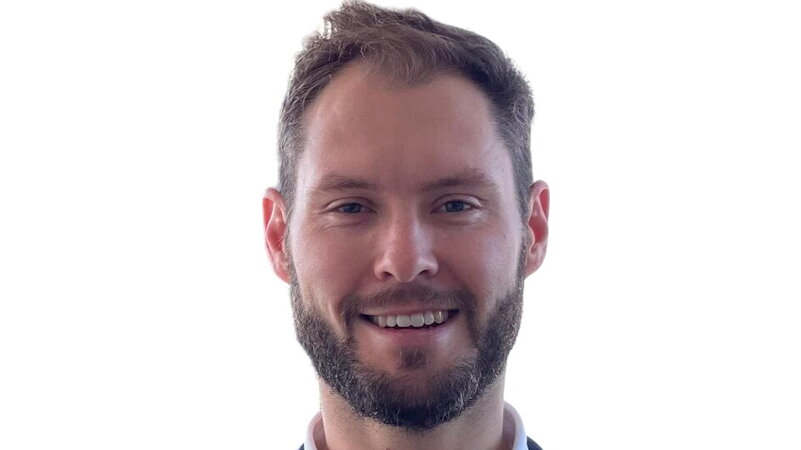
For a company like Pirelli, “everything” covers a lot more than just moving materials and products from place to place – it also includes keeping a close watch on geopolitical matters as well as economic trends, because in the supply-chain world there is no such thing as a distant event.
Marco is a raw material planning manager in the Milan headquarters of the company, who sees all of this from the centre of the Pirelli supply-chain operation. One of his main concerns is to build up the resilience of the supply chain to cope with logistics shocks, such as the blocking of the critical Suez Canal sea route when the container ship Ever Given ran aground in 2021.
The need for resilience
“One way we are improving resilience is through information,” says Marco, who studied mechanical engineering before joining Pirelli. “The more information you have, the faster you can react and the better you can minimise the impact of disruptions. When the Suez Canal was blocked, it was taking a lot of time for companies to find out where their shipments were. Our team here in Milan has put in a lot of effort to create new tools that can automatically track the whereabouts of all our shipments and to understand what routes they are going to follow according to what is happening in the world.
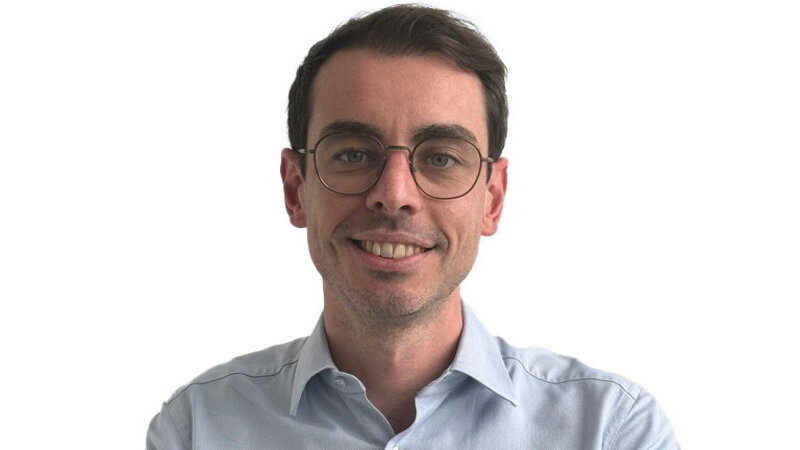
“The fact is you always have to have a backup plan,” adds Marco. “You should never rely on one solution, you should always have a Plan B – and a Plan C and a Plan D as well.”
Pirelli recognises a need for resilience right through its global supply chain, because in the end customers, wherever they are, want to be able to rely not just on product quality, but on product delivery too. In addition, some customers have very particular requirements and special supply-chain arrangements may be necessary for them.
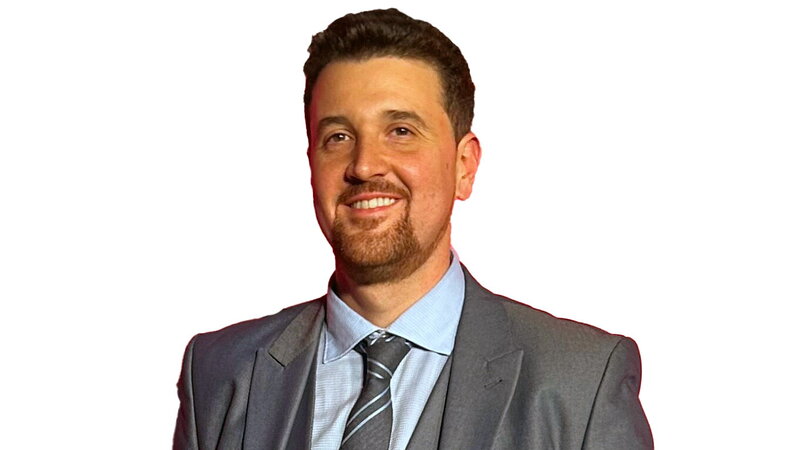
Building the customised supply chain
Achieving perfection in this case meant building a customised supply chain for Formula One®. For one thing racing tyres are very sensitive to temperature extremes, so they have to be shipped at precisely controlled temperatures. Then the packaging had to be completely redesigned for transporting as airfreight, as Vincenzo explains. “We usually don't ship by airfreight, but for Formula One®, with its very tight timelines, it can be necessary. And that meant we had to find the best way to pack tyres on to a Boeing 737 cargo plane. We came up with a new pyramid structure that allowed us to get more tyres in the cargo bay. As a result, we only had to use one cargo plane instead of two, reducing cost and, of course, reducing emissions.”
Behind such levels of customisation and resilience lies day-to-day efficiency. And for Alessandra, a production planning manager in Milan, it's all about making sure operations are running smoothly.
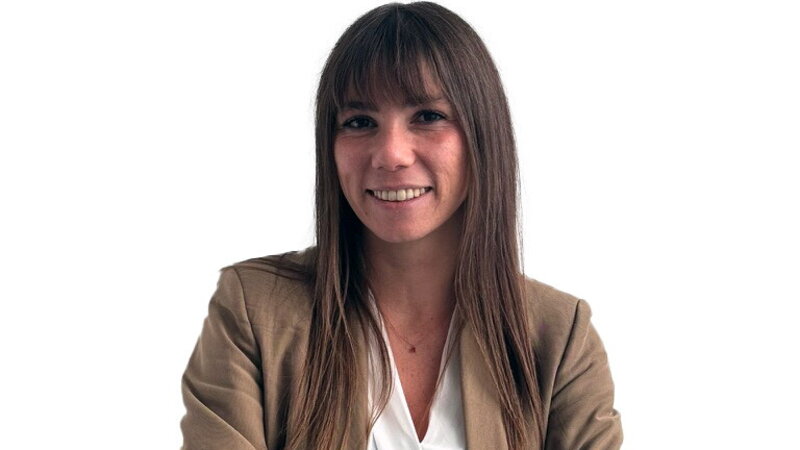
An efficient machine
“We are trying to maximise the fulfilment of customer demand in an efficient way for production and the use of resources,” says Alessandra. That means monitoring production and delivery dashboards on a daily basis, and being ready to act fast if things are not going to plan. “We might see that we are missing a scheduled consignment from a particular plant and I need to get on the phone and establish what the issue is,” adds Alessandra, a management engineering graduate. “I need to know whether it is a production process issue, or whether we need to repair machinery, or get substitute products from a different source. Then I need to know what commitments we have with the relevant customer – do we need to work with them to solve the issue. Supply chain is about dealing with a lot of uncertainties – and being efficient is about resolving those uncertainties.”
Supply-chain roles call for the ability to analyse data, communicate well and be proactive and decisive. Like most people working in supply chain, Alessandra says that the key to success is flexibility. “The environment changes all the time,” she says. “If you want to do the same thing day in day out, then it's not the job for you. Every day is different. “And one thing is for sure: it's not boring.”