This is not a scene you are likely to see at Nobu, even at its most contemporary.
A sushi chef takes requests at an elegant cedar counter and induces robots to 3D print exquisitely crafted morsels. Premium tuna nigiri made from cultured cells. Uni sculpted by laser from powdered urchin. Eel whose texture is recreated as a bundle of micro-threads that blend with the sweet tare sauce.
The chef provides only the final touches – perhaps a squirt of yuzu citrus – and the artistic presentation.
It may sound futuristic, or even preposterous, but the Sushi Singularity project, which includes Yamagata University, a leading research institution, and major corporations such as chipmaker Advantest, plans to launch just such a restaurant in Tokyo as early as 2020. The audacious idea is that 3D printing can reinvent food for both aesthetic and altruistic ends – perfecting texture and flavour, fine-tuning nutritional content and helping to end food scarcity and preserve fish stocks. It is 3D printing's ability to replicate complex structures – such as honeycomb and lattice – and different types of density and concentration that gives it unique advantages in one day making lab-grown food taste natural.
New directions
The project run by the Japanese conceptual design studio Open Meals is among a host of 3D printing initiatives – from nutrition to medicine and industrial design – that are stretching the boundaries of a technology that a few years ago appeared to be losing steam.
Predictions of a new industrial revolution, which would allow people to print their way to materialistic paradise, turned out to be premature. Buyers of $2,000 3D printers found they could do little more than create pretty replicas of Buckingham Palace or Elvis Presley, a far cry from scenarios of people printing their own clothes, furniture or cars. Meanwhile, ethical concerns over misuse of the technology, such as terrorists printing automatic rifles, began to tarnish the image of the field, and efforts to regulate 3D manufacturing of firearms have proven tricky.
Yet in fact, 3D printing innovation has been surging forward in tandem with a salutary decline in hype. Breakthroughs in the range of materials that can be used for 3D printing, for example, are enabling surprising new applications in advanced manufacturing.
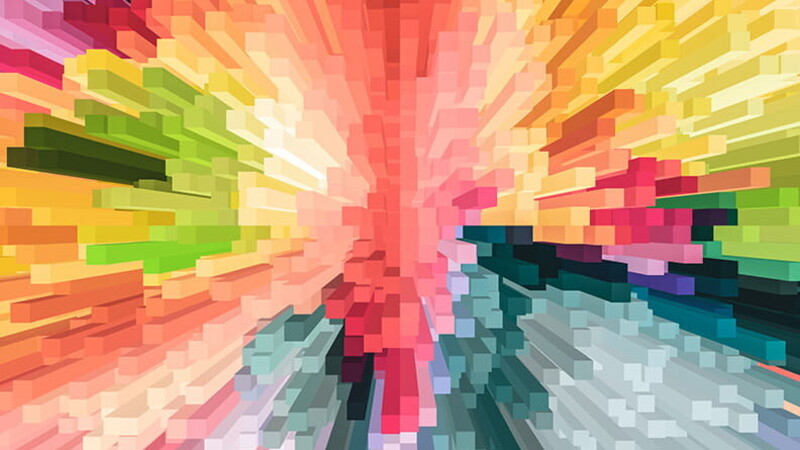
Industry interest
Pirelli first started experimenting with 3D printing in the late 1990s, but research began in earnest in the last decade as the technology improved. It has tested the process to produce some plastic parts and has used metallic powders in 3D printing techniques to help create moulds and other equipment for tyre production. Further developments are expected as the technology and related materials continue to improve and become more economical.
While most industrial uses of 3D printing are for prototyping or proof of concept models, it is increasingly found in the production of advanced components. BMW's i8 Roadster uses a 3D printed mounting for its top cover , making it lighter and stronger. And GE Aviation deploys additive manufacturing – also known as 3D printing – to produce fuel nozzles at its plant in Alabama.
Meanwhile, Adidas has launched an elite running shoe with a 3D printed midsole created by Silicon Valley start-up Carbon , which uses digital light projection to shape liquid resin into a latticed structure that offers superior cushioning. Perhaps most importantly, the method reconciles mass production with custom crafting: the buyer's foot can be scanned for on-the-spot printing of a personalised shoe.
But for now, at least, momentum comes more from cutting-edge technologies than mass-market approaches, in areas that include tissue engineering and personalised nutrition.
Printing a healthier future
Scientists are turning living cells into “bio-ink” and printing them layer by layer on to tiny scaffolds to generate complex tissue models. Researchers at Princeton University have used 3D printing to produce a bionic ear – fusing tissue with electronics – that goes beyond auditory restoration to capture radio frequencies beyond the human range.
Elsewhere, Canadian researchers last year developed a hand-held device that brings hope to severe burns victims by printing skin tissue, according to a Smithsonian article , as easily as “rolling out Scotch tape”. Meanwhile, a team at the University of Utah reported that they have successfully developed a technique to 3D print ligaments and tendons, promising much faster recovery times for patients with muscle injuries
Prosthetics is one of the most promising fields for medical 3D printing. Scientists are rapidly refining techniques to print eyes, noses and limbs for people who have lost them to disease or injury, or were born without them.
And a US company is mass-producing dental and joint implants that are superior to conventional ones. 3D layering allows them to be crafted into complex shapes with internal morphology, and given a porous surface that encourages bone to grow into the implant.
The ultimate personalisation
While not immune to showmanship, Sushi Singularity has more serious ambitions of helping to solve global problems – including ending hunger, improving hospital care and providing dietary guidance to extend lives. The platform plans soon to upload biometric and genomic data that will be analysed to craft individualised menus matching each diner's health profile.
“Hyper personalisation will become common for future foods,” Open Meals says on its website. “Based on DNA, urine and intestinal tests, people will have individual health IDs. This identity is analysed and nutritional matching performed.”
Bon appétit!