Artificial intelligence (AI) and neural networks play an important role in the innovative tyre development at Pirelli. These are the significant milestones connected with the opening of the new Development Center and the inauguration of the static simulator at its Breuberg site in Hesse (Germany), where Pirelli employs 2500 employees in the whole country, including 250 engineers among them.
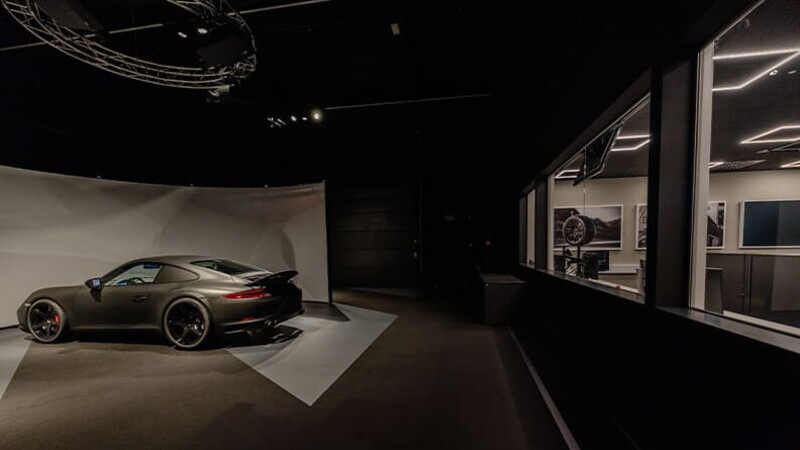
VIRTUAL SIMULATION TO BE FASTER AND MORE SUSTAINABLE
The new Virtual Development Center will enable the premium tyre manufacturer to develop and test products virtually for cars that do not yet exist in reality. Such progress results in considerable advantages for Pirelli and its OEM customers in the automotive industry. Tyre development times are reduced by up to 30 percent, and the tyre manufacturer needs to produce around 30 per cent fewer physical prototypes. This not only saves time and money but also makes a significant contribution to sustainable production. Pirelli has set itself the goal of achieving CO2-neutral production by 2030. Furthermore, the driving simulator, as part of the virtual tire development process, enables Pirelli to achieve increasingly more precise results compared with traditional methods. It is also a way to provide solutions that are increasingly in line with the requirements of car manufacturers.
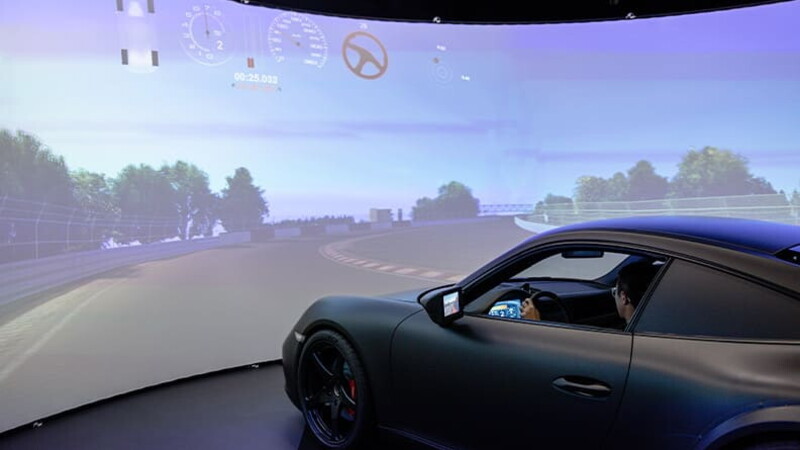
VIRTUAL TESTING TYRE PERFORMANCE ALSO FOR ELECTRIC CARS
Pirelli engineers can “take the wheel” of virtual versions of any vehicle model loaded into the simulator by the car manufacturers. Test drives then begin with the virtual tyre models. The engineers see how the vehicle's behaviour is affected or should be affected by steering, acceleration, and braking manoeuvres in the virtual vehicle. The virtually tested tyres are for combustion engines as well as Elect technology tyres for electric cars and plug-in hybrids.
The combination of high-tech simulation, artificial intelligence, and expert engineering paves the way for Pirelli to enter a new era of mobility.