Over 200 people involved in around 80 projects with 18 universities and 24 strategic partners across the entire world in the most highly varied fields: from manufacturing processes to materials, from cyberspace to tyre dynamics, to the use of ever more sophisticated tools for virtualisation and simulation. These are the numbers from Pirelli's Open Innovation model, based on the exchange of ideas, resources and technological capabilities with the world of external research. A world that links in with and completes the group's Research and Development department, which relies on 13 internal research centres with over 2,100 employees world-wide.
It is thanks to this constant decanting of expertise and know-how that Pirelli – constantly on the lookout for innovative solutions and always the most advanced technologies – succeeds in meeting the challenges imposed by the scenario of mobility and of the automotive industry. It is in this way that numerous agreements have been created with centres of excellence, collaborative networks and strategic partnerships in order to promote projects capable of accelerating the search for innovative solutions and of contributing to the leadership position held by Pirelli in High Value production. A virtuous circle which puts universities in contact with Pirelli's industrial development process and brings new ideas and resources to the company, in a continuous exchange of experience and expertise.
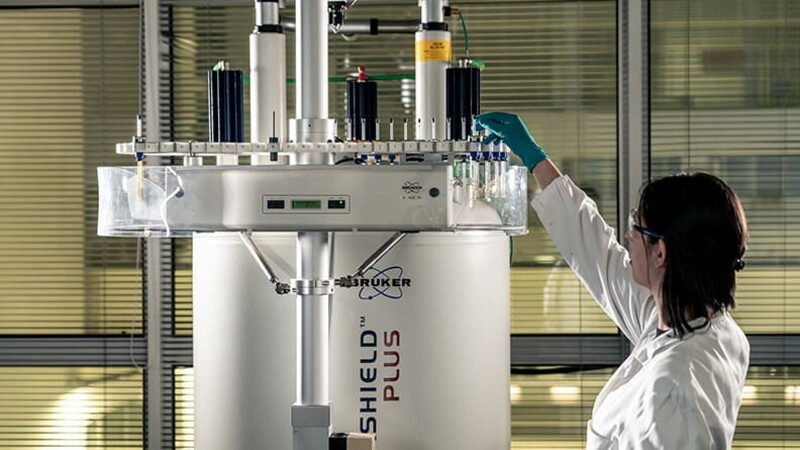
Amongst the most important Open Innovation projects, those holding a particular relevance today relate to virtualisation and to sustainability. The latter, in particular, brings ever more challenging objectives which also affect research and experimentation with materials. Indeed, between now and 2030, Pirelli expects to use, on certain selected product lines, more than 60% of materials from renewable sources, progressively reducing those of fossil origin. Examples include silica derived from rice husks, materials derived from the treatment of tyres at the end of their life, such as powder, regenerated and recovered Carbon Black, but also bio fillers such as lignin and sepiolite, plasticisers/resins of plant origin, and certain textile strengtheners using fibres from renewable sources. All these are innovative materials or from completely natural sources which make up part of a tyre.
Furthermore, the use of virtual models, which will allow us to reduce the development time for new products by 30%, the annual cost of prototypes by 20% and the set-up time for new production lines by 30%, contributes to an increase in sustainability.
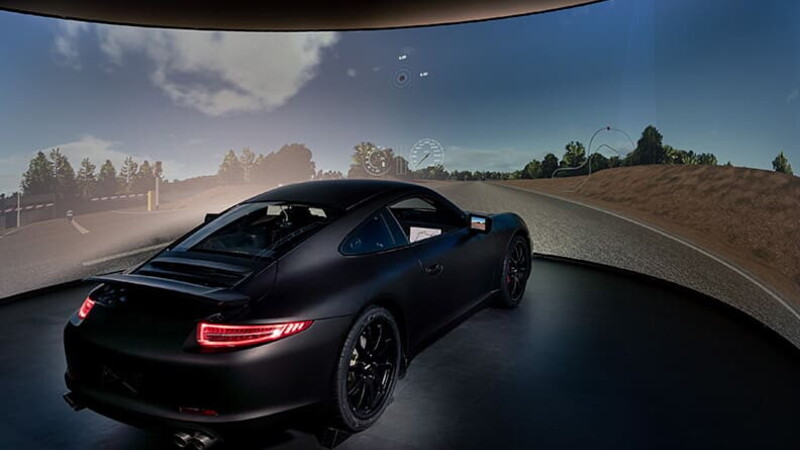
It was indeed thanks to the collaboration with the most important research institutes that the new simulator was established at its location in the Pirelli research and development centre in Milan. A success not just in terms of sustainability but of product performance, given that such a system is favourable to a collaboration with the most important car manufacturers during the development phase. The simulator, in fact, is the first point of encounter, albeit a virtual one, between vehicle models in their design phase and the prototype tyres which will need to be fitted to them in the future. This allows us to reduce development times and also to match more rapidly the performance of the tyres to the characteristics of the cars.
These are just some of the examples of the numerous Open Innovation research projects at Pirelli. It is a fundamental model from the era of Industry 4.0, of a flexible and intelligent manufacturing facility which has to find rapid solutions to constantly changing problems, where focus on technology and on innovation is extremely high and where the response to the requirements of customers, be they car manufacturers or end consumers, needs to correspond to specific innovative customisations, in line with Pirelli's “perfect fit” philosophy.