Minimal development times, fewer prototypes to dispose of and greater collaboration with car manufacturers. These are the principal outcomes which Pirelli hopes to achieve thanks to the new static simulator which was inaugurated in the Research & Development centre in Milan.
30% LESS TIME TO DEVELOP TYRES
With this new technology, the average time to develop new tyres, for both road and motor sports use, can be reduced by approximately 30%, thanks to the use of virtual prototypes of various car models. Indeed, thanks to the simulation, the parameters can be modified quickly during the development, and the information about the tyres and vehicles can be exchanged quickly with car manufacturers. Compared with more traditional design methods, the virtual model of the car received from the car manufacturer can be installed on this simulator, or it can be reproduced internally; moreover, joint design and development activities can be carried out on the car maker's simulator too, in order to be perfectly in line with the development time frames of the car manufacturers, who produce new models at an increasingly faster rate.
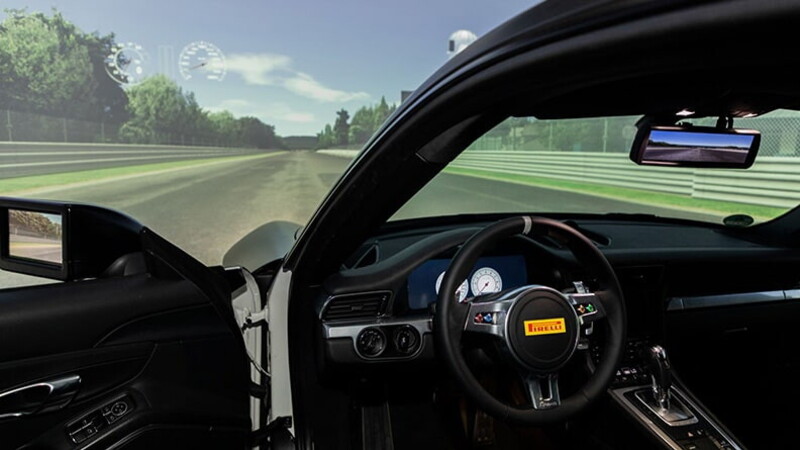
MORE ENVIRONMENTAL SUSTAINABILITY
Furthermore, the use of this new test process makes it possible to reduce the annual production of physical tyre prototypes, in accordance with Pirelli's vision of sustainability, with ensuing environmental benefits.
F1 TECHNOLOGY ON THE ROAD
Simulation has already been used in designing and testing Formula 1 tyres and for other motor sports categories for the last 10 years. Now this technology and the experience accrued by Pirelli's R&D department is also being applied to tyres intended for road use.
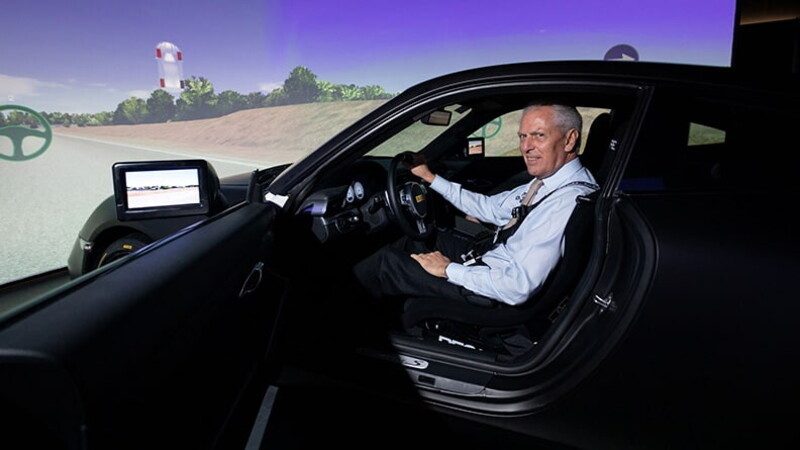
A MAXI SCREEN AND A CAR FOR ALL THE WORLD'S CIRCUITS
The simulator consists of a cylindrical screen with an extension of 210° and a 7.5 m diameter to reproduce visually the various circuits and driving conditions. The system features a static car in the centre of the screen, equipped with some active technologies to replicate the real behaviour of the car for the driver, including: the seat, the steering wheel, the safety seatbelts and several shakers placed where the suspension and engine would be. Every operation is coordinated by a control room, where the parameters of the various tyre and vehicle technical specifications can be introduced, and the results of the simulated tests can be monitored, including: forces upon tyre contact with the road and all the performance indexes of the tyre, in addition to the tester's subjective assessment.
NOT JUST STATIC, BUT ALSO DYNAMIC SIMULATION
The activity carried out on this simulator is integrated with the dynamic simulator project which reproduces the lateral and longitudinal accelerations, in addition to the rotations, and which will be installed at the Milan Polytechnic University, a facility with whom Pirelli has for some time collaborated, and thanks to which additional tests are carried out as a supplement to those currently conducted in the Pirelli research centre in Milan.